Introduction
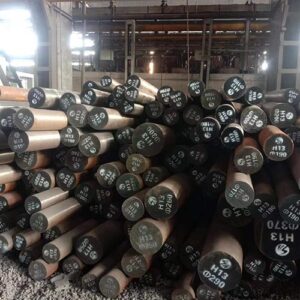
In the realm of modern manufacturing, the choice of materials plays a pivotal role in determining the quality, durability, and efficiency of products. One such material that has significantly impacted various industries is H13 tool steel. Renowned for its exceptional properties, H13 tool steel has become a cornerstone in the production of molds, dies, and other critical components across a multitude of applications. In this blog post, we delve into the profound impact of H13 steel on modern manufacturing processes.
Understanding H13 Tool Steel: Properties and Composition
Before delving into its impact, it’s essential to grasp the fundamental properties and composition of H13 tool steel. H13 is a chromium-based hot-work tool steel known for its excellent combination of high toughness and resistance to thermal fatigue. Its composition typically includes chromium, molybdenum, vanadium, and other alloying elements, which impart superior mechanical properties such as high hardness, wear resistance, and dimensional stability.
Applications Across Industries
The versatility of H13 tool steel makes it indispensable across various industries. From automotive to aerospace, and from consumer goods to industrial machinery, H13 finds applications in diverse manufacturing processes. Let’s explore some key sectors where the impact of H13 steel is profound:
- Injection Molding: H13 steel is extensively used in injection molding due to its high hardness and thermal conductivity. Its ability to withstand repeated heating and cooling cycles makes it ideal for producing precision molds with intricate designs.
- Extrusion Dies: In the extrusion industry, where metals or plastics are shaped into specific profiles, H13 steel’s exceptional hot hardness and resistance to thermal fatigue ensure prolonged tool life and consistent product quality.
- Die Casting: Die casting, a manufacturing process for producing metal parts with high accuracy, relies on H13 tool steel dies for their resistance to heat checking and thermal cracking, ensuring reliable performance in high-pressure casting environments.
- Forging Dies: H13 steel’s combination of toughness and high-temperature strength makes it a preferred choice for forging dies, enabling the production of forged components with precise dimensions and surface finish.
- Extrusion Tooling: Whether it’s for aluminum, copper, or other metals, extrusion tooling made from H13 steel offers exceptional thermal conductivity and wear resistance, resulting in efficient extrusion processes and superior product quality.
Advantages and Limitations
While H13 tool steel offers a plethora of advantages, it’s essential to acknowledge its limitations as well. Let’s take a closer look at the pros and cons:
Advantages | Limitations |
---|---|
High hardness | Susceptible to decarburization during heat treatment |
Excellent wear resistance | Moderate machinability |
Superior thermal conductivity | Limited availability in certain regions |
Resistance to thermal fatigue | Relatively high cost compared to some alternatives |
Innovations and Advancements
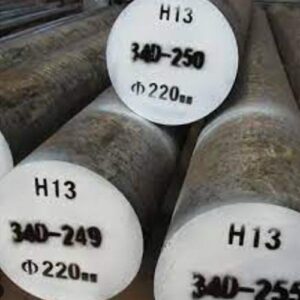
The continuous evolution of manufacturing processes has led to ongoing innovations in H13 tool steel production and utilization. Advanced heat treatment techniques, such as vacuum hardening and cryogenic treatment, enhance the material’s properties, further expanding its applicability in demanding manufacturing environments. Additionally, research into alloy modifications aims to address the material’s limitations and unlock new possibilities for improved performance and cost-effectiveness.
Conclusion
In conclusion, the impact of H13 tool steel on modern manufacturing cannot be overstated. Its exceptional properties, coupled with a wide range of applications, have revolutionized various industries, enabling the production of high-quality components with precision and efficiency. While challenges exist, ongoing research and development efforts continue to drive innovation, ensuring that H13 steel remains at the forefront of material choices for critical manufacturing processes.
FAQ
Q:What are the primary alloying elements in H13 tool steel?
A:H13 tool steel typically contains chromium, molybdenum, vanadium, and other alloying elements.
Q:What is the maximum operating temperature for H13 steel?
A:H13 steel can withstand temperatures up to approximately 540°C (1000°F) during continuous operation.
Q:Is H13 tool steel suitable for high-pressure applications?
A:Yes, H13 tool steel’s resistance to thermal fatigue makes it well-suited for high-pressure applications such as die casting and extrusion.
Q:How does H13 steel compare to other tool steels in terms of cost?
A:While H13 steel may have a relatively higher cost compared to some alternatives, its superior properties often justify the investment in critical manufacturing applications.
Q:Can H13 tool steel be welded?
A:Yes, H13 tool steel can be welded using conventional methods, although preheating and post-weld heat treatment may be necessary to minimize the risk of cracking and ensure proper mechanical properties.
This comprehensive guide provides insights into the significance of H13 steel in modern manufacturing, highlighting its advantages, applications, and ongoing advancements. As industries continue to evolve, H13 tool steel remains a cornerstone material, driving innovation and enabling the production of tomorrow’s technologies.