Introduction
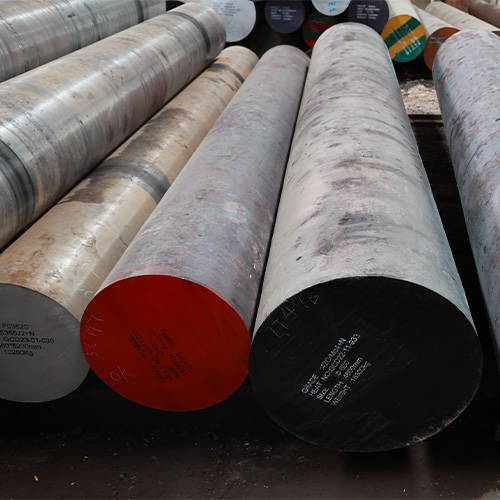
Alloy 4140 steel, a versatile medium-alloy steel, is renowned for its exceptional strength, toughness, and wear resistance. Its unique composition, including chromium and molybdenum, provides an excellent balance of properties, making it a preferred choice for a wide range of applications in industries such as automotive, aerospace, and manufacturing. In this comprehensive guide, we will delve into the characteristics, applications, and heat treatment processes of Alloy 4140 steel.
The Composition and Properties of Alloy 4140 Steel
Alloy 4140 is a medium-alloy steel, characterized by its moderate amount of alloying elements. These elements, primarily chromium and molybdenum, contribute significantly to its exceptional properties:
- Chromium: Enhances corrosion resistance, hardness, and wear resistance.
- Molybdenum: Improves toughness, strength, and hardenability.
- Carbon: Contributes to hardness and strength.
The combination of these elements gives Alloy 4140 steel a unique set of properties, including:
- High Strength: Alloy 4140 can be heat-treated to achieve very high tensile strengths, making it suitable for applications requiring exceptional load-bearing capacity.
- Good Toughness: It offers a balanced combination of strength and toughness, ensuring resistance to impact loads and sudden stresses.
- Excellent Wear Resistance: The presence of chromium and molybdenum contributes to its wear resistance, making it ideal for components subjected to abrasive conditions.
- Good Machinability: Alloy 4140 is relatively easy to machine, reducing manufacturing costs and improving production efficiency.
- Hardenability: It can be hardened to a deep depth, making it suitable for large components that require uniform hardness throughout.
Applications of Alloy 4140 Steel
Alloy 4140 steel’s versatility makes it a valuable material in various industries:
- Automotive: Crankshafts, connecting rods, gears, axles, and other highly stressed components.
- Aerospace: Landing gear components, engine mounts, and structural parts.
- Manufacturing: Dies, punches, and tooling for metal forming processes.
- Oil and Gas: Drilling tools, pump shafts, and other components subjected to high loads and corrosive environments.
- Construction: Structural components, such as beams and columns, where strength and durability are critical.
- Agricultural Equipment: Implements and machinery that require high strength and wear resistance.
- Mining and Excavation: Components for heavy-duty equipment, such as drills and excavators.
- Power Generation: Turbine shafts and other components in power plants.
Heat Treatment of Alloy 4140 Steel: Tailoring Properties
Heat treatment is crucial for achieving the desired properties in Alloy 4140 steel. The most common process is quench and temper, which involves:
- Heating: Heating the steel to a specific temperature (usually 1500°F to 1650°F) to form austenite.
- Quenching: Rapidly cooling the steel in oil or water to form martensite, a hard and brittle phase.
- Tempering: Reheating the steel to a lower temperature (typically 300°F to 1000°F) to relieve internal stresses and improve toughness.
The specific heat treatment cycle can be adjusted to achieve different combinations of hardness, strength, and toughness. For example, a higher tempering temperature will result in lower hardness but improved toughness.
Microstructure and Properties of Alloy 4140 Steel
The microstructure of Alloy 4140 steel is significantly influenced by the heat treatment process. The primary microconstituents include:
- Martensite: A hard and brittle phase formed during quenching.
- Bainite: A tough and ductile phase formed at lower cooling rates.
- Ferrite: A soft and ductile phase that may be present in some microstructures.
The relative amounts of these microconstituents determine the mechanical properties of Alloy 4140 steel.
Comparison of Alloy 4140 with Other Steels
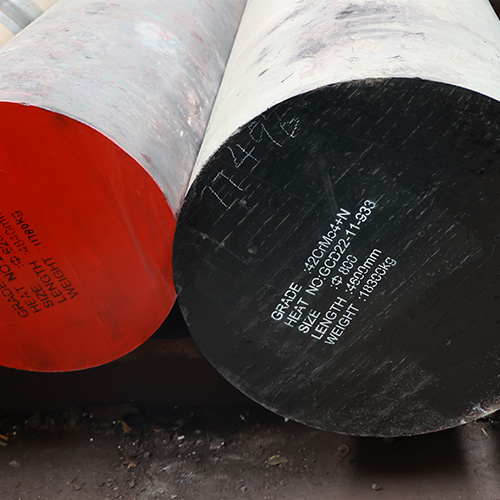
Steel Grade | Carbon Content | Alloying Elements | Typical Applications |
---|---|---|---|
4140 | 0.40% | Cr, Mo | Automotive, aerospace, manufacturing |
1045 | 0.45% | None | General-purpose steel, shafts, gears |
4340 | 0.40% | Ni, Cr, Mo | High-strength applications, aircraft components |
4130 | 0.30% | Cr, Mo | General-purpose steel, shafts, gears |
Conclusion
Alloy 4140 steel is a versatile and high-performance material that finds applications in a wide range of industries. Its exceptional strength, toughness, and wear resistance, coupled with its good machinability, make it a preferred choice for engineers and manufacturers seeking reliable and durable materials. By understanding the properties and applications of Alloy 4140 steel, engineers can make informed decisions when selecting materials for their projects.
FAQ
What is the difference between Alloy 4140 and 4340 steel?
While both are high-strength alloys, 4340 contains additional nickel, which improves its toughness and fatigue strength.
Can Alloy 4140 steel be welded?
Yes, Alloy 4140 can be welded, but proper welding procedures and post-weld heat treatment are essential to prevent cracking and distortion.
What is the best heat treatment for Alloy 4140 steel?
The optimal heat treatment depends on the desired properties and the specific application. Consult a metallurgist or heat treatment specialist for tailored recommendations.
Is Alloy 4140 steel magnetic?
Yes, Alloy 4140 steel is magnetic, as it is primarily composed of iron.