Introduction
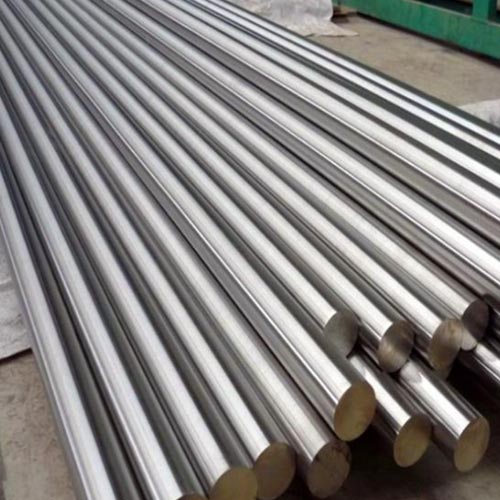
Steel processing plays a crucial role in determining the quality and durability of steel products. The intricate methods involved in shaping, treating, and finishing steel influence its mechanical properties, performance, and longevity in various applications. This article delves into the various stages of steel processing, examining how each phase affects the final product’s quality and durability.
The Importance of Steel Processing
Steel processing encompasses a wide range of operations, including melting, casting, rolling, heat treatment, and finishing. Each step is critical in ensuring that the final product meets the required specifications and standards. The quality of the steel product is often directly linked to how effectively these processes are executed.
Key Stages of Steel Processing
-
Melting and Refining
- The initial phase involves melting raw materials and refining the steel to remove impurities. This stage sets the foundation for the subsequent processing stages.
-
Casting
- Once the steel is melted and refined, it is cast into molds. The casting process can significantly influence the internal structure of the steel, affecting its strength and durability.
-
Rolling
- Steel rolling transforms the cast steel into usable forms, such as sheets or bars. This process affects the grain structure and mechanical properties of the steel.
-
Heat Treatment
- Heat treatment involves heating and cooling the steel to alter its physical properties. This stage is vital for enhancing strength, hardness, and ductility.
-
Finishing Processes
- The final touches, including surface treatment and coating, enhance the steel’s appearance and protect it from corrosion and wear.
Summary of Steel Processing Stages and Their Impact on Quality
Processing Stage | Key Impact on Quality | Potential Risks |
---|---|---|
Melting | Purity and composition | Inclusion of impurities |
Casting | Internal structure | Defects like porosity |
Rolling | Grain orientation | Warping or inconsistent thickness |
Heat Treatment | Hardness and toughness | Overheating or cracking |
Finishing | Surface integrity | Poor adhesion of coatings |
The Role of Temperature in Steel Processing
Temperature control is paramount in steel processing. Each stage requires precise temperature management to achieve the desired results. Deviations from optimal temperatures can lead to significant quality issues.
Melting and Casting Temperatures
During melting, steel is typically heated to around 1,500°C. This high temperature ensures complete melting and mixing of alloying elements. In casting, cooling rates must be controlled to prevent defects.
Rolling and Heat Treatment Temperatures
In the rolling process, the temperature influences the steel’s ductility. Hot rolling occurs at temperatures above the steel’s recrystallization temperature, enhancing workability. Conversely, heat treatment temperatures must be carefully monitored to achieve the desired hardness without compromising ductility.
The Impact of Alloying Elements
Alloying elements are added during steel processing to improve specific properties. The choice and proportion of these elements significantly influence the final product’s quality and durability.
Common Alloying Elements
- Carbon: Increases hardness and strength but can reduce ductility if too high.
- Chromium: Enhances corrosion resistance and hardness.
- Nickel: Improves toughness and ductility.
- Manganese: Increases hardness and helps with deoxidization.
Effects of Alloying Elements on Steel Properties
Alloying Element | Effect on Hardness | Effect on Ductility | Effect on Corrosion Resistance |
---|---|---|---|
Carbon | Increases | Decreases | Minimal |
Chromium | Increases | Slightly decreases | Significantly increases |
Nickel | Moderate increase | Increases | Moderate increase |
Manganese | Increases | Decreases | Minimal |
Quality Control Measures in Steel Processing
Implementing rigorous quality control measures throughout the steel processing stages is essential to ensure product quality and durability. From raw material selection to final inspections, each step must adhere to strict standards.
Key Quality Control Techniques
- Chemical Analysis: Ensuring the right composition of alloying elements through regular testing.
- Mechanical Testing: Assessing the strength, hardness, and ductility of steel samples.
- Non-Destructive Testing (NDT): Detecting internal defects without damaging the steel product.
- Surface Inspection: Checking for surface defects, such as cracks or improper coatings.
Common Issues in Steel Processing
Despite careful management, various issues can arise during steel processing, impacting product quality and durability.
Defects and Their Implications
- Porosity: Small voids within the steel can weaken the material and lead to premature failure.
- Cracking: Can occur during casting or heat treatment if temperatures are not controlled properly.
- Inclusions: Non-metallic materials trapped in the steel can compromise mechanical properties.
Common Defects and Their Effects on Steel Quality
Defect | Description | Impact on Durability |
---|---|---|
Porosity | Void spaces in steel | Reduced strength |
Cracking | Fractures in material | Immediate failure risk |
Inclusions | Impurities within the steel | Brittle fracture |
The Future of Steel Processing
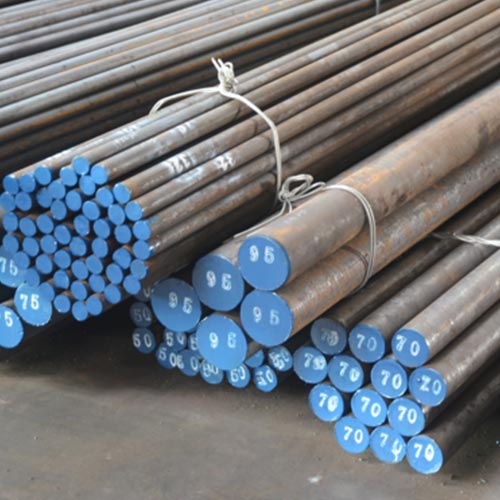
As technology advances, steel processing methods are evolving. Innovations such as automation, advanced materials, and new processing techniques are changing the landscape of steel manufacturing.
Trends in Steel Processing
- Automation and AI: Increasing efficiency and consistency in production.
- Sustainable Practices: Minimizing environmental impact through better recycling and energy efficiency.
- Advanced Alloys: Developing new alloy compositions for enhanced performance.
Conclusion
Steel processing is a complex yet vital aspect of steel production that directly impacts product quality and durability. Understanding the nuances of each processing stage allows manufacturers to produce steel that meets or exceeds industry standards. As the industry evolves, continuous improvement in steel processing techniques will be essential to maintain product quality and adapt to changing market demands.
FAQ
Q:What is steel processing?
A:Steel processing refers to the various methods used to transform raw steel into finished products, including melting, casting, rolling, and heat treatment.
Q:How does temperature affect steel quality?
A:Temperature plays a critical role in determining the mechanical properties of steel. Precise temperature control is necessary at each stage of processing to avoid defects and ensure optimal quality.
Q:Why are alloying elements important in steel processing?
A:Alloying elements are added to enhance specific properties of steel, such as strength, hardness, and corrosion resistance, which significantly impact the quality and durability of the final product.
Q:What common defects can occur during steel processing?
A:Common defects include porosity, cracking, and inclusions, each of which can adversely affect the strength and durability of steel products.
Q:How do quality control measures improve steel processing?
A:Quality control measures ensure that every stage of the steel processing adheres to strict standards, reducing the risk of defects and ensuring the final product meets quality requirements.