Introduction
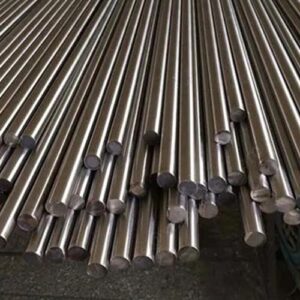
Stainless steel is renowned for its corrosion resistance properties, making it a popular choice in various industries, from architecture to marine engineering. Among the different grades of stainless steel, 316 stainless steel stands out for its exceptional resistance to corrosion, particularly in harsh environments. In this blog post, we delve into the corrosion resistance of 316 stainless steel, exploring its properties, applications, and factors influencing its performance.
Properties of 316 Stainless Steel
316 stainless steel, also known as marine-grade stainless steel, is an austenitic stainless steel alloy containing chromium, nickel, and molybdenum. These alloying elements contribute to its superior corrosion resistance, even in chloride-rich environments such as coastal areas and industrial settings. The following table summarizes the key properties of 316 steel:
Property | Value |
---|---|
Composition | 16-18% Chromium, 10-14% Nickel, 2-3% Molybdenum |
Corrosion Resistance | Excellent resistance to corrosion in various environments, including chlorides |
Temperature Range | -50°C to 800°C (-58°F to 1472°F) |
Tensile Strength | 515 MPa (74,700 psi) |
Yield Strength | 205 MPa (29,700 psi) |
Density | 8.00 g/cm³ |
Factors Influencing Corrosion Resistance
While 316 stainless steel offers exceptional corrosion resistance, several factors can influence its performance in different environments. These factors include:
- Exposure to Chlorides: Chloride ions, commonly found in seawater and industrial chemicals, can accelerate the corrosion of stainless steel. However, the molybdenum content in 316 steel enhances its resistance to chloride-induced corrosion.
- Temperature: Elevated temperatures can affect the corrosion resistance of stainless steel. While 316 steel maintains its integrity at high temperatures, prolonged exposure to extreme heat can lead to sensitization and subsequent corrosion.
- Surface Finish: The surface finish of stainless steel plays a crucial role in its corrosion resistance. Smooth, polished surfaces are less susceptible to corrosion than rough surfaces, as they minimize the accumulation of contaminants and promote passive film formation.
Applications of 316 Stainless Steel
Due to its superior corrosion resistance and mechanical properties, 316 stainless steel finds widespread applications across various industries, including:
- Marine Engineering: Components exposed to seawater, such as ship fittings, offshore platforms, and marine hardware, rely on the corrosion resistance of 316 steel to withstand harsh marine environments.
- Chemical Processing: Equipment used in chemical processing plants, including reactors, pipelines, and storage tanks, often utilize 316 steel due to its resistance to corrosive chemicals and acids.
- Food and Beverage Industry: 316 steel is preferred for food processing equipment, brewing tanks, and pharmaceutical machinery, where hygiene and corrosion resistance are paramount.
Testing and Evaluation
Corrosion testing is essential to assess the performance of 316 stainless steel in specific environments and applications. Common testing methods include salt spray testing, electrochemical impedance spectroscopy (EIS), and immersion testing. By subjecting samples to simulated service conditions, engineers and researchers can evaluate the material’s corrosion resistance and predict its long-term durability.
Comparison of 316 Stainless Steel and 420 Stainless Steel
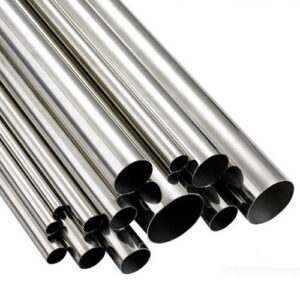
Property | 316 Stainless Steel | 420 Stainless Steel |
---|---|---|
Composition | 16-18% Chromium, 10-14% Nickel, 2-3% Molybdenum | 12-14% Chromium, <1% Molybdenum, <1% Nickel |
Corrosion Resistance | Excellent resistance to corrosion in various environments, including chlorides | Moderate corrosion resistance; susceptible to corrosion in certain environments |
Hardness | Typically lower hardness, around 25-30 HRC | Higher hardness, typically 50-55 HRC |
Strength | Lower tensile and yield strength, suitable for general-purpose applications | Higher tensile and yield strength, suitable for applications requiring high strength and hardness |
Toughness | Higher toughness, better impact resistance | Lower toughness, more brittle behavior |
Applications | Marine engineering, chemical processing, food and beverage industry | Toolmaking, surgical instruments, cutlery, firearms |
Conclusion
The corrosion resistance of 316 stainless steel makes it an invaluable material in industries where exposure to corrosive environments is a concern. With its superior properties and versatility, 316 steel continues to be a preferred choice for critical applications in marine, chemical, and food processing industries. Understanding the factors influencing its corrosion resistance and employing appropriate testing methods are essential for maximizing the performance and longevity of components made from 316 stainless steel.
FAQ
Q: Is 316 stainless steel suitable for outdoor applications?
A: Yes, 316 stainless steel is highly suitable for outdoor applications, including architectural structures, railing systems, and signage, thanks to its excellent resistance to atmospheric corrosion and chloride-induced corrosion.
Q: How does 316 steel compare to other stainless steel grades in terms of corrosion resistance?
A: 316 steel offers superior corrosion resistance compared to many other stainless steel grades, particularly in chloride-rich environments. However, it may not be as resistant to certain acids and chemicals as higher alloyed stainless steels such as 904L.
Q: Can 316 stainless steel be welded?
A: Yes, 316 stainless steel is readily weldable using conventional welding techniques. However, post-weld heat treatment may be required to restore corrosion resistance in the heat-affected zone.
Q: What maintenance is required for 316 stainless steel components?
A: Routine cleaning and inspection are recommended to maintain the corrosion resistance and aesthetic appearance of 316 stainless steel components. In harsh environments, periodic passivation treatments may be necessary to restore the passive oxide layer.
In conclusion, 316 stainless steel exemplifies the balance between corrosion resistance, mechanical strength, and affordability, making it a preferred material for a wide range of applications. Understanding its properties, applications, and testing methods is essential for ensuring the reliability and longevity of components exposed to corrosive environments.